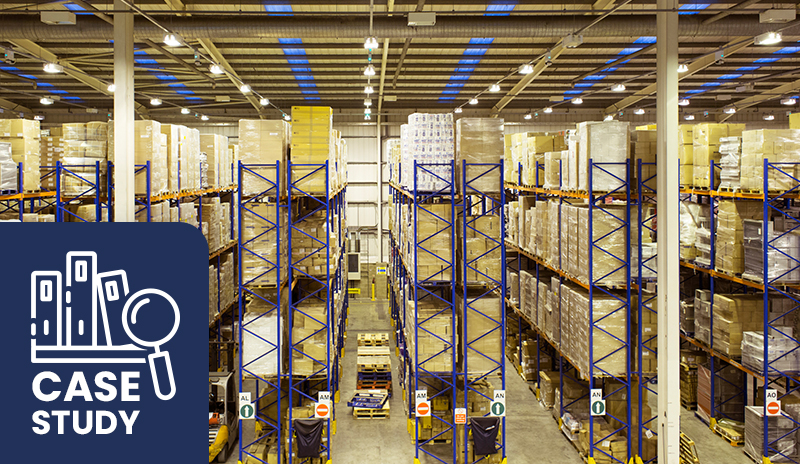
Introduction
In the United Kingdom, cold storage and transportation companies play a vital role in ensuring the integrity of perishable goods while maintaining the highest standards of energy efficiency. This case study explores the implementation of an Elcomponent Energy Monitoring System in a leading UK-based cold store and transport company to enhance energy management and reduce operational costs. The company’s name has been anonymised for confidentiality reasons
Challenges
The client faced several challenges:
- Rising energy costs and a need to reduce operational expenses.
- Limited insight into energy consumption and areas of inefficiency.
- Ensuring compliance with environmental regulations and sustainability goals.
- Maintaining the quality and safety of stored goods.
- A desire to optimise energy consumption without compromising operational efficiency.
Solution
The client opted to implement the Elcomponent Energy Monitoring System, a comprehensive energy management solution tailored to the unique needs of the cold storage and transportation industry.
System Installation
- The Elcomponent team of experts installed a range of energy monitoring equipment within the client’s cold storage facilities. This included meters, data loggers, and real-time monitoring software.
- Data Collection and Analysis
- The Elcomponent system gathered real-time data on energy consumption across the client’s operations.
Key metrics included:
- Energy consumption of refrigeration units
- Electricity, Gas and Water
- Reporting and Dashboards
The Elcomponent software (MW2) provided the client with detailed reports and recommendations. These insights allowed the company to identify areas of energy wastage, optimise equipment usage, and develop energy-efficient protocols.
Results
The implementation of the Elcomponent Energy Monitoring System yielded significant results:
- Energy Savings: The client achieved a substantial reduction in energy consumption and costs, resulting in an estimated annual saving of £120,000. This saving was due to optimising the performance of refrigeration units and adopting more energy-efficient practices.
- Environmental Benefits: By reducing energy consumption, the client decreased its carbon footprint. This aligns with the UK’s environmental regulations and sustainability goals, improving the company’s reputation as an environmentally responsible business.
- Improved Product Quality: With accurate temperature and humidity monitoring, the client experienced fewer incidents of temperature deviations. This led to a decrease in product spoilage and improved overall product quality.
- Operational Efficiency: The company’s operations became more streamlined and efficient. Real-time data allowed for better route planning, load management, and vehicle maintenance, reducing operational downtime and costs.