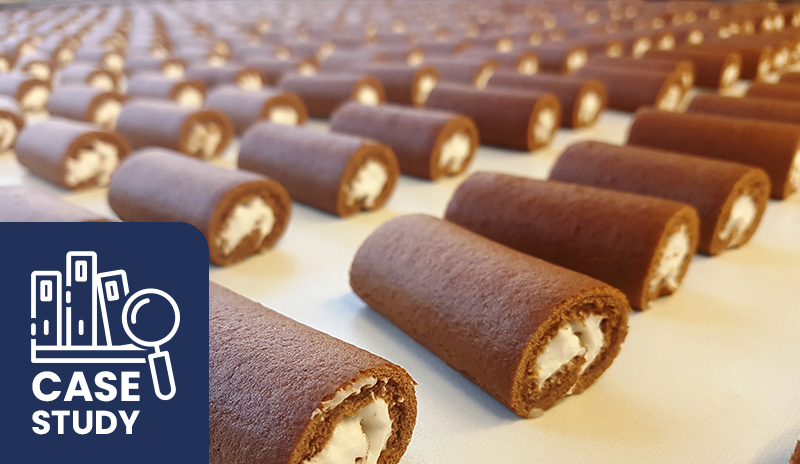
Introduction
The Client owns a number of processing factories, and is a leading organisation in the food industry, has long been committed to improving operational efficiency and reducing its environmental footprint. Recognising the importance of energy consumption in their production process, the management decided to implement an energy monitoring system to gain better control over their energy usage and make informed decisions for sustainability and cost savings.
Challenges
The Client was facing several challenges related to energy management, including:
Inadequate Energy Data: The factory lacked a comprehensive system to monitor energy consumption, which made it difficult to identify inefficiencies or opportunities for optimisation.
High Energy Costs: The rising cost of energy was impacting the factory’s operational expenses, cutting into profit margins.
Sustainability Goals: The company aimed to reduce its carbon footprint and align with environmental sustainability goals.
Regulatory Compliance: Compliance with energy usage regulations and reporting requirements was becoming increasingly complex.
Solution
The factory management decided to address these challenges by installing an advanced Energy Monitoring System (EMS) from Elcomponent with the following components:
- Electricity, Gas and Water Meters: Communicating meters were installed across critical points in the factory to measure real-time energy consumption accurately.
- Data Acquisition System: Data acquisition units were employed to collect, process, and store energy consumption data from smart meters.
- Software Platform: A user-friendly software platform was implemented to provide real-time data visualisation, historical data analysis, and reporting capabilities.
Implementation Process
The installation of the Energy Monitoring System followed these steps:
- Assessment and Planning: A team of experts conducted an energy audit to identify the most critical areas for monitoring and set up a detailed plan for implementation.
- Equipment Selection and Installation: meters were selected based on the specific needs of the factory and strategically placed. Data acquisition units and software were installed and configured.
- Training and Integration: Factory personnel received training on using the software platform and integrating the EMS with existing systems.
- Real-time Monitoring: With the system in place, real-time energy dashboards became available for analysis and decision-making.
Results
The implementation of the Energy Monitoring System led to significant improvements in the factory’s energy management:
- Cost Reduction: By identifying energy inefficiencies and optimising energy usage during peak hours, the factory reduced its energy costs by 5% within the first year.
- Sustainability: The EMS allowed the factory to reduce its carbon emissions and aligning operational activity with its sustainability goals.
- Operational Efficiency: Real-time data and alerts helped the factory’s maintenance team respond to issues more rapidly, reducing downtime.
- Regulatory Compliance: Providing accurate data for the clients regulatory reporting
Future Plans
The Client is now considering further enhancements to their EMS, including the integration of production data to provide predictive energy consumption based on factory output. Expansion on the other sites is underway, and similar results are expected at each.